Flame Spraying is a cost-effective thermal spraying process that produces quality coatings and as it is relativity low energy, can be used to spray substrates that cannot be exposed to high temperatures.
The powdered spray materials is melted during a chemical reaction between oxygen and a fuel combustion thus creating a heat source. The sprayed material is projected towards the surface at high speed with the use of compressed air, accelerating towards and on to the surface.
The Flame spray process can progress to a second step of ‘fusing’. This gives dense and well-bonded coating on the surface similar to tough, high-stress wear characteristics of a hardface weld overlay.
Fusing of flame-sprayed coatings involves heating and coating to its melting point, strengthening the bond between the coating and the substrate. A flame is usually applied to heating the coating. Fusing takes place at temperatures between 950°C and 1250°C, producing a wet shine on the surface resulting in fusing the coating within itself and to the substrate, thereby achieving a true metallurgical bond.
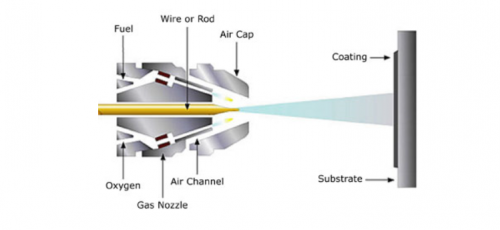
Benefits of Flame Spraying
- ‘Cold’ process as the substrate temperature can be kept low giving flexibility to spray substrates that cannot be exposed to high temperatures
- Cost effective process
- Provides low stress coatings therefore thick coatings can be applied
- Used for repairs of high cost components
Benefits of Fusing
- Eliminates porosity found in flame sprayed coatings
- Gives dense, homogennous and strong coatings with good resistance properties.
- Creates a true metallurgical bond
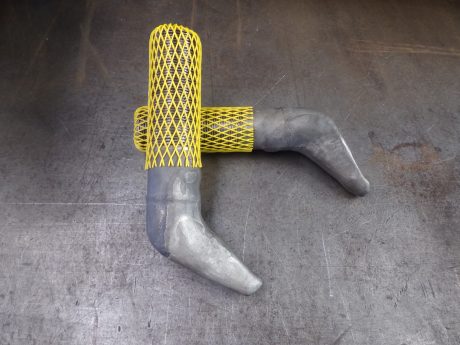
Flame Spraying Coatings Characteristics:
- Very low stress coatings, therefor allowing very thick coatings to be applied.
- Corrosion Resistance
Fusing Coating Characteristics:
- Extremly hard, coatings can be applied with a hardness up to 80Rc.
- Metallurgical bond of coating to substrate
- Resistant to impact and chipping
- Corrosion resistant
- Minimized distortion and oxidization
.
Materials deposited
- Nickel
- Chromium
- Cobalt
- Boron
- Iron
- Tungsten
- Tungsten Carbide
In varying blends
Industries
- Power generation
- Oil and gas processing
- Steel rolling
- Pump and valve manufacture
.